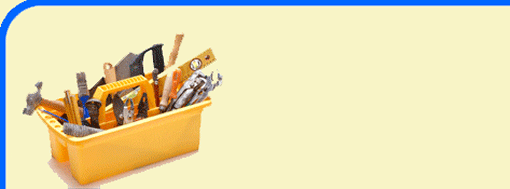
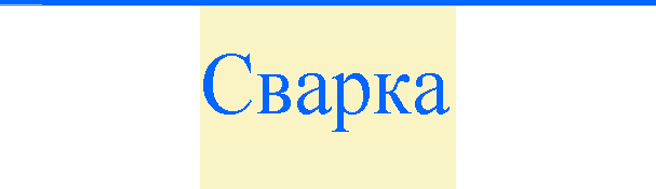
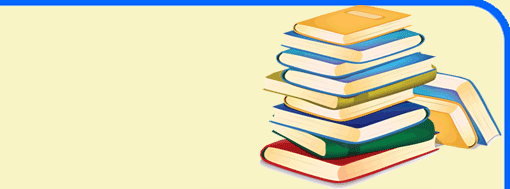
- Главная
- Автомобили
- Велосипед
- Глоссарий
- Инструмент
- Крепеж
- Металлообработка
- Оснастка и приспособления
- Соединения
- Товары
Аргонодуговая сварка — разновидность дуговой сварки.
При аргонодуговой сварке электрическая дуга зажигается в атмосфере инертного газа — аргона. В высокотемпературной зоне горения дуги аргон, будучи тяжелее воздуха, вытесняет его из зоны сварки и блокирует окисление сварного шва.
Аргонодуговая сварка применяется в основном для изделий из алюминиевых и титановых сплавов, жаропрочных и нержавеющих сталей, латуней и бронз.
При сварке крупногабаритных деталей на некоторых производствах применяют камеры наполненные аргоном. Сварщики в таких камерах работают в космических скафандрах. Воздух для дыхания в скафандры подается по шлангам.
Применение аргонодуговой сварки обеспечивает получение высокопрочных и вакуумопрочных швов, при толщине свариваемых деталей — от десятых долей до нескольких десятков миллиметров.
Диффузионная сварка основана на использовании явления диффузии.
![]() |
1. Силовой механизм |
2. Рабочая камера |
3. Оправки |
4. Свариваемый материал |
Свариваемые детали с тщательно зачищенными свариваемыми поверхностями помещаются в рабочую камеру. В рабочей камере создается разрежение путем откачки атмосферного воздуха до давления 10‾5мм рт. ст. Для повышения пластичности и ускорения процесса диффузии на свариваемые детали прикладывается небольшое сдавливающее усилие и они нагреваются до температуры 600 — 800°С. Продолжительность процесса сварки составляет около 5мин.
В результате нагрева свариваемых деталей в вакууме происходит интенсивное очищение поверхностей от окислов и органических загрязнений. Сварные швы, полученные в результате диффузионной сварки, при высоком качестве не имеют внутренних напряжений.
Методом диффузионной сварки возможно получить соединения большинства металлов, а также соединения керамических деталей и соединения металлов с керамикой.
Промышленное применение диффузионной сварки ограничено наличием сложного дорогостоящего оборудования и невысокой производительностью, обусловленной временем откачки рабочей камеры, временем нагрева деталей, временем процесса диффузии, временем охлаждения.

Дуговая сварка, при которой свариваемый материал нагревается до температуры плавления с использованием электрической дуги.
Свариваемое изделие (обычно металлическое) включается непосредственно в цепь электрической дуги, играя роль одного из электродов. Другой электрод при этом бывает плавящимся, по химическому составу обычно близким к свариваемому металлу или неплавящимся, изготовленным преимущественно из графита, вольфрама или угля.
Дуговую сварку можно производить и при косвенном нагреве. В этом случае свариваемое изделие, не будучи включённым в электрическую цепь, нагревается электрической дугой между двумя неплавящимися электродами. В случае косвенного действии электрической дуги нагревание менее интенсивно, чем при нагреве дугой прямого действия. Преимуществом косвенного нагрева является возможность сваривать диэлектрические материалы, например, стекло, керамику, пластмассу.
Нередко дуговую сварку проводят в среде аргона, двуокиси углерода или гелия. В этом случае при нагреве свариваемых материалов не происходит их окисление кислородом воздуха.
Конденсаторная сварка — разновидность контактной сварки.
При проведении конденсаторной сварки свариваемые материалы нагреваются до температуры плавления под воздействием электрического тока, получаемого при разряде батареи конденсаторов.
При контактном методе сварки импульс тока разряда конденсатора протекает через свариваемые детали, которые предварительно сжаты. В месте контакта деталей возникает сварочная электрическая дуга, с помощью которой происходит сварка. Малое время сварки (1,5 — 3,0мс) при токе сварки достигающим 15 000А позволяет получать надежное сварное соединение с очень малым участком термического влияния. В зоне сварки отсутствует коробление свариваемого материала и на материалах отсутствуют цвета побежалости, характерные для точечной сварки.
При ударном методе сварки электрическая дуга и разряд конденсатора возникают в момент соударения свариваемых деталей друг с другом. Время сварки в данном случае составляет максимум 1,5мс, что в свою очередь делает зону термического влияния еще меньше. Данный метод сварки может быть рекомендован для сварки деталей из цветных металлов и сплавов с большой теплопроводностью.
Контактная сварка — особый вид сварки, при которой происходит интенсивный местный нагрев в местах контакта соединяемых деталей при прохождении через них электрического тока.
При контактной сварке особенно большое сопротивление проходящему току возникает в месте контакта свариваемых деталей. Поэтому примыкающая к нему область металла разогревается особенно интенсивно. Разогретые и часто оплавленные детали сдавливаются, в результате чего образуется прочное соединение.
К контактной сварке относят стыковую сварку, точечную и роликовую.
Для соединения металлических деталей небольшой толщины, не превышающей 5 — 6мм, используется преимущественно точечная сварка. Соединяемые детали зажимают между электродами и через них пропускают ток. Место соединения деталей, сварная «точка» напоминающая заклепку, диаметром соответствующая диаметру электрода в интервале 4 — 10мм. При сварке деталей больших размеров ставится множество сварных точек, которые обеспечивают достаточную прочность соединения. Точечная сварка нашла широкое применение в автомобильном производстве, самолетостроении, в производстве различных приборов и машин, металлической посуды.
В стыковой сварке, которая совмещает контактную, дуговую и сварку давлением, разогрев основного металла производится с использованием электрической дуги. Для исполнения стыковой сварки детали соединяют с небольшим усилием. Затем через свариваемые детали пропускают электрический ток большой силы при низком напряжении. После этого свариваемые детали очень медленно разводятся до появления между ними электрической дуги. Под воздействием дуги поверхности обеих деталей разогреваются. После достаточного разогрева свариваемые детали сжимаются с очень высоким усилием. При производстве стыковой сварки получается чистое и крепкое сварное соединение.
При роликовой сварке предназначенные для соединения детали протягиваются между электродами, выполненными в форме роликов. На электроды подаются очень быстро повторяющиеся импульсы электрического тока. При этом создается серия накладывающихся друг на друга сварных точек, которые формируют непрерывный сварной шов.
![]() |
1. Глухое зеркало |
2. Активный элемент |
3. Полупрозрачное зеркало |
4. Лампа накачки |
5. Отражатель |
6. Источник питания |
7. Система оптического контроля |
8. Фокусирующие линзы |
9. Обрабатываемый материал |
Лазерная сварка — процесс, при котором свариваемые материалы нагреваются до температуры плавления с помощью сфокусированного лазерного излучения.
Лазерное излучение — электромагнитное излучение в основном оптического диапазона, создаваемое лазером. От излучения других источников света отличается высокой когерентностью, малой угловой расходимостью, высокой яркостью. Такие свойства излучения дают возможность получить в фокусе линзы высокую плотностью энергии порядка 108 Вт/см2.
Для целей сварки используются твердотельные лазеры, работающие на алюмоиттриевом гранате, активированном Nd, работающие как в импульсном, так и в непрерывном режиме. Длина волны излучения этих лазеров составляет 1,06мкм, что позволяет для фокусировки использовать обычную стеклянную оптику. Мощность излучения этих лазеров доходит до 1кВт. Источником накачки такого лазеров служит газоразрядная лампа. К. п. д. этого лазера 4 — 5%.
Широкое применение также получили газовые СО2-лазеры. Эти лазеры работают в основном в непрерывном режиме. Применение получили лазеры с продольной прокачкой, мощность излучения которых составляет несколько кВт и лазеры с поперечной прокачкой, мощность излучения которых 20кВт и выше. Длина волны излучения лежит в ближней инфракрасной области и составляет 10,6мкм. Для фокусировки излучения с такой длиной волны используются кристаллы из NaCl (поваренная соль), GaAs, Ge. Для накачки этих лазеров используется газовый разряд. К. п. д. составляет 10%.
Высокая плотность энергии лазерного излучения и высокие скорости нагрева в процессе сварки обуславливает небольшие объемы расплавленного металла в зоне сварного шва. Благодаря этому процесс лазерной сварки характеризуется небольшой зоной термического влияния, минимальные деформации в околошовной зоне, высокую конструкционную и технологическую прочность в сварных соединениях.
Микроплазменная сварка — разновидность плазменной сварки.
При микроплазменной сварке, используется высокая степень ионизации газа. В плазмотроне применяются вольфрамовые электроды диаметром 1–2мм. При таких условиях плазменная дуга горит при весьма малых токах, от 0,1А.
Специальный плазмотрон для микроплазменной сварки позволяет получить плазменную дугу диаметром около 2мм. Это позволяет сконцентрировать тепло в локальной области свариваемого изделия и прогревать только зону сварки, без повреждения соседних участков. Применяя микроплазменную сварку можно весьма эффективно сплавлять изделия малой толщины, до 1,5мм.
Основным защитным и плазмообразующим газом является аргон. В зависимости от конкретных условий сварки к нему может добавляться водород, увеличивающий эффективность процесса сварки.
Микроплазменная сварка нашла большое применение в производстве тонкостенных емкостей и труб, при приварке сильфонов и мембран к массивным деталям, соединении термопар, в ювелирном производстве.
Плазменная сварка — специализированный вид дуговой сварки, в которой для нагрева сварного шва используется плазменная струя.
Плазма, т. е. поток высокоионизированного газа создается в особой горелке — плазмотроне. Для того чтобы повысить температуру и мощность обычной дуги и превратить ее в плазму используются процессы сжатия дуги с вдуванием в нее плазмообразующего газа. Струя плазмы, исходящая из плазмотрона, ускоряется и сжимается под воздействием электромагнитных сил. При этом она оказывает на свариваемое изделие как термическое, так и газодинамическое воздействие. Температура в плазменной струе достигает 40000°С.
Существуют следующие схемы процесса плазменной сварки:
сварка производится плазменной дугой, горящей между изделием и неплавящимся электродом внутри плазмотрона;
и плазменной струей, которая выдувается из плазмотрона потоком газа, когда дуга зажжена между соплом плазмотрона и неплавящимся электродом.
Поток горячей плазмы создает неплохую защиту зоны сварки. В случае необходимости сварной шов можно защитить дополнительным потоком защитного газа.
Термокомпрессионная сварка — технология соединения деталей из металлов и неметаллов.
Для получения качественного соединения один из соединяемых материалов должен иметь достаточно высокую пластичность.
Процесс термокомпрессионной сварки аналогичен процессу холодной сварки. При термокомпрессионной сварке детали, находящиеся в нагретом состоянии, сжимают с помощью специального инструмента. В месте соединения происходит пластическая деформация, которая обеспечивает получение надежного соединения. При этом взаимная деформация деталей гораздо ниже, чем при холодной сварке.
![]() |
1. Верхний электрод |
2. Свариваемый материал |
3. Нижний электрод |
4. Магнитострикционный преобразователь |
Pос — осадочное давление |
P — усилие сжатия |
Ультразвуковая сварка основывается на использовании механических колебаний с частотой 15—170 кГц.
При таком способе сварки к местам соединения свариваемых поверхностей с помощью волновода или посредством металлического стержня подводят ультразвуковые колебания, возбуждаемые магнитострикционным преобразователем. При ультразвуковой сварке прочное соединение формируется при объединенном воздействии на свариваемые детали механических колебаний и небольших сжимающих нагрузок.
Этот метод позволяет соединять фольгу со стеклом и керамикой, сваривать листы фольги из чистого алюминия, меди, серебра и золота, а также тонкие проволочки из этих металлов и их сплавов с металлическими плёнками и полупроводниковыми материалами. Кроме того, с помощью ультразвука можно получить сварные соединения из ниобия, вольфрама и молибдена, из многих термопластичных полимеров, в частности полистирола.
Ультразвуковая сварка применяется при присоединении кристаллов к корпусам полупроводниковых приборов, подсоединения выводов к кристаллам диодов и транзисторов, при беспроволочном монтаже интегральных схем.
Холодная сварка — способ сварки за счет пластической деформации без дополнительного нагрева.
Решающую роль в процессе холодной сварки играют пластические деформации, роль которых заключается в максимальном утончении и удалении слоев оксидов на сопрягаемых поверхностях свариваемых деталей. При этом свариваемые поверхности сближаются до расстояний соизмеримых с параметрами кристаллической решетки, где начинают оказывать влияние силы межатомного взаимодействия с возможностью создания устойчивых химических связей.
Наиболее распространенным видом холодной сварки является точечная сварка. Ее применяют для сварки алюминия, меди с алюминием, армирования алюминия медью. При этом способе свариваемые детали устанавливают между двумя пуансонами, которые сжимаются с усилием, обеспечивающим пластическую деформацию деталей и создание сварного соединения.
![]() |
1. Электронно-лучевая пушка |
2. Сварочная камера | |
3. Свариваемый материал | |
4. Электронная линза | |
5. Пучок электронов |
Электронно-лучевая сварка, при которой свариваемый материал нагревается до температуры плавления пучком электронов.
Поток электронов создается специальным устройством — электронной пушкой. Электроны, двигаясь в вакууме со скоростями до 165000км/сек, ударяются о металлическую поверхность. При этом кинетическая энергия электронов переходит в тепловую энергию.
Процесс электронно-лучевой сварки производится в вакуумной камере, из которой откачан воздух до давления 10–4 — 10–6мм рт. ст. Наличие вакуума позволяет электронам беспрепятственно достигать свариваемого металла, и защищает сварной шов от окисления.
Пучок электронов, сфокусированный электронной линзой до размера 0,01 — 0,1мм позволяет применять этот способ сварки при герметизации металлостеклянных корпусов электровакуумных приборов, в технологии микроэлектроники, а также для сварки химически активных, тугоплавких, и разнородных материалов.
Скажите “спасибо” автору.